模內熱切模具在世界各工業發達地區均得到廣泛的應用。
1、模內澆口分離自動化,降低對人的依賴度;傳統的塑膠模具開模后產品與澆口相連,需二道工序進行人工剪切分離,模內熱切模具將澆口分離提前至開模前,消除后續工序,有利于生產自動化,降低對人的依賴。
2、降低產品人為品質影響;在模內熱切模具成型過程中,澆口分離的自動化保證澆口分離處外觀一致性,其結果是品質一致的零件,而傳統人工分離澆口工藝無法保證澆口分離處外觀一致。因此市場上很多高品質的產品均由模內熱切模具生產。
2.1 模內切裝置基本構成與系統布局
如圖1、2所示,一般模內切裝置主要由下列關鍵部件組成:
切刀:主要負責分離澆口料,一般使用SKH51做熱處理加硬。
導向塊:與切刀配合實現導向及產品成型,一般使用S136做熱處理加硬。
微型油缸:承受高油壓推動切刀向上動作。
復位彈簧:當切刀向上完成切斷動作后,系統進行泄壓,此時復位彈簧施力切刀復位。
行程開關:設置于分型面,用于給高壓時序控制器發送開合模信號。
高壓時序控制器:輸出高壓油,通過高壓油管和模具油路給微型油缸供力及控制動作實施時間
2.2 基本原理與動作實現
注塑產品射膠—保壓期間,利用高壓時序控制器提供高壓油路推動微型油缸,微型油缸推動切刀頂出切斷產品澆口料,也就是在產品注塑成型的過程中進行分離。依據產品級模具結構不同,可以調整高壓時序控制器及刀具形狀, 達到的分離效果。
3澆口設計
使用模內熱切的澆口與傳統澆口有些區別,常用的有牛角澆口轉切口和側進澆口轉切口兩種,設計方面需要注意以下問題:
3.1 澆口的大小設計
澆口的大小對注塑產品的澆注效果影響很大,在兼顧澆注效果的同時,也需滿足切刀的標準化和可換性問題。對于澆口的長度和寬度,需要按澆注需求選擇接近規格的切刀型號。對于澆口的厚度,依據模內切裝置高壓油缸的行程值(可穩定切斷的狀態),可在0~4mm之間選擇和調整。
3.2 溢料槽的設計
由于需要擠壓剪切實現分離澆口料,必須設計溢料槽分流由于切刀擠壓成型產生位移的塑料,避免澆口局部塑料密度增大而導致切刀過快磨損或者切不干凈。溢料槽通常為切刀外側面(內側面為注塑產品)一個比流道寬的槽位,參考尺寸為:寬度=流道寬+5mm,高度與流道等高。各相接棱邊必須倒好R角,做到各面圓滑過渡,同時需要做大出模角度,防止局部粘模而導致水口料頂出不平衡。
4 應用場合
模內熱切應用場合廣泛,適用于側水口,搭接式水口,大型扇形水口,環形水口,潛水口,牛角水口等均可應用。刀口形狀根據澆口形狀變化而變化,同時依據不同的澆口在刀口 |
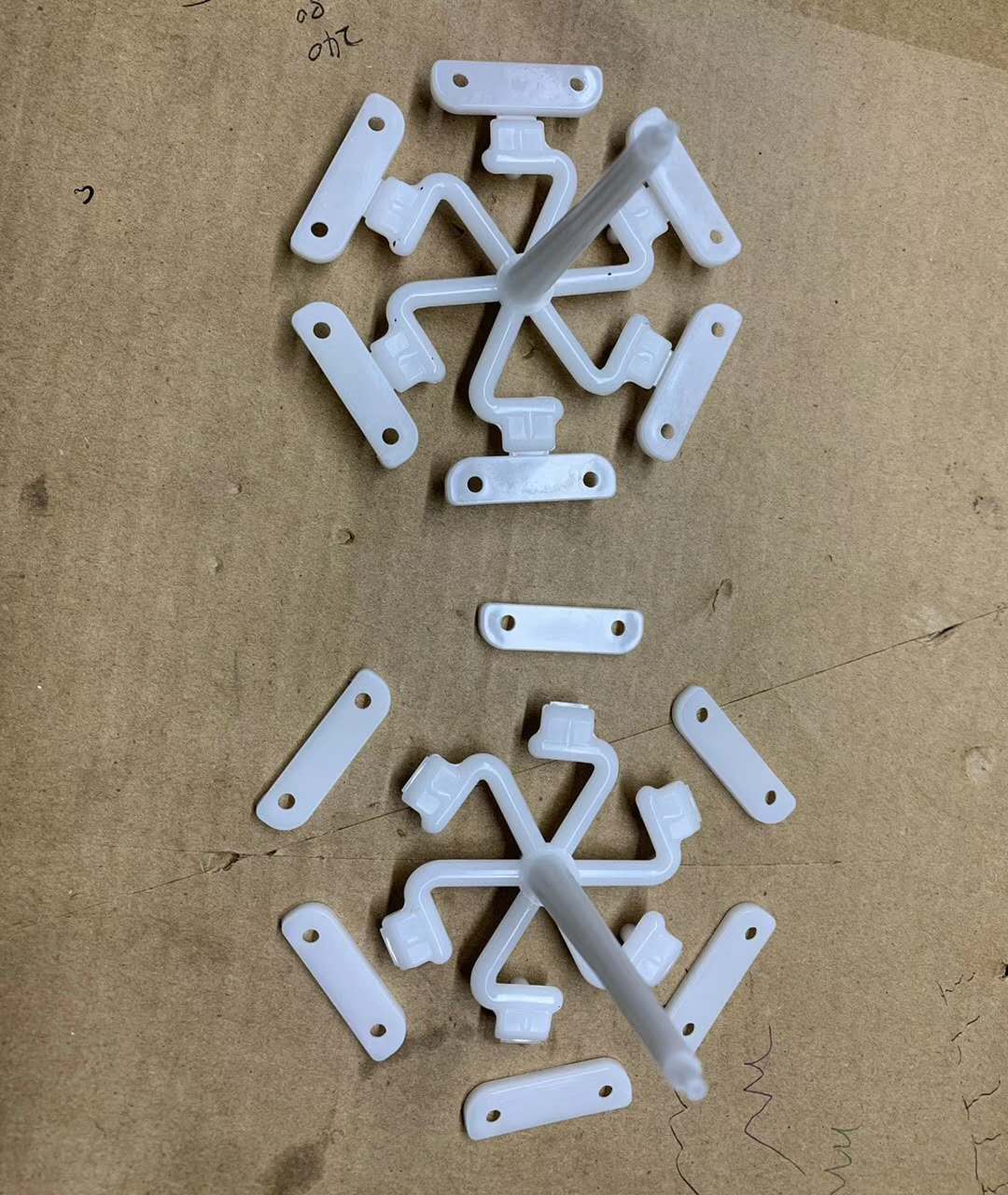 |
|